Can a small improvement dramatically change the quality of the final product? If it is one, probably not. But if there are many of them, and they have a common vector, quality can change dramatically. Sometimes continuous small changes within a project prove to be better and more effective than a massive re-engineering of all business processes on new rails.
Below we will talk about one of the well-known management methodologies that can be applied not only in companies or project teams, but also in personal life. We are talking about Kaizen planning.
What is kaizen planning
Kaizen (Japanese: 改善, literally translated as ‘improve good’ or ‘change for the better’) is not exactly a methodology, but rather a philosophy or practice based on continuous improvement of the processes around us, wherever they may be: at work, at home, in production, in business, in a team….
When we talk about kaizen as a management methodology (the term kaizen planning is often used), it can be classified as a lean methodology. Read more about Lean Project Management.
Kaizen has been used in business planning for a long time, even during the rebuilding of Japan in the post-war years. Many large companies adopted it. And in 1986, the first book by Masaaki Imai was published. It was he who gave the kaizen concept the impetus to spread around the world. As a result, Masaaki is traditionally regarded as the founder of all lean concepts.
In the 2000s, kaizen began to be actively applied to software product development.
The aim of kaizen planning is to achieve a perfect balance between quality, cost and logistics (as an analogue in personal life: expectations, budget/cost and time).
Kaizen Planning Basics
If you study several sources describing the kaizen approach, you will suddenly find that different terms, principles and so on are used everywhere.
Why does this happen? It’s quite simple. Kaizen is a philosophy. It has no clear postulates. During its existence, the theoretical basis itself has undergone a number of changes. Only the main objective of kaizen remains unchanged.
What exactly are the principles of the Kaizen philosophy? Only those principles that are stated in the official books written by the author, Masaaki Imai. For example:
- Kaizen: The Key to Japan’s Competitive Success
- Gemba Kaizen: A Commonsense, Low-Cost Approach to Management
- Strategic Kaizen. Using Flow, Synchronization, and Leveling Assessment to Measure and Strengthen Operational Performance
Kaizen concepts for companies
The basic concept of Kaizen for business consists of the following key elements:
- Focus on process continuity.
- Maintenance and improvement.
- Adherence to the ‘Plan, Do, Check and Impact’ and ‘Standardise, Do, Check, Impact’ cycles.
- Emphasis on quality.
- Every user of a business process is considered a customer.
- It is imperative to collect, analyse and verify data (facts) for improvement.
Let’s talk about each of these in a little more detail.
Innovate, improve and sustain the business according to current management roles
There should be an approximate balance between the main functions and the position.
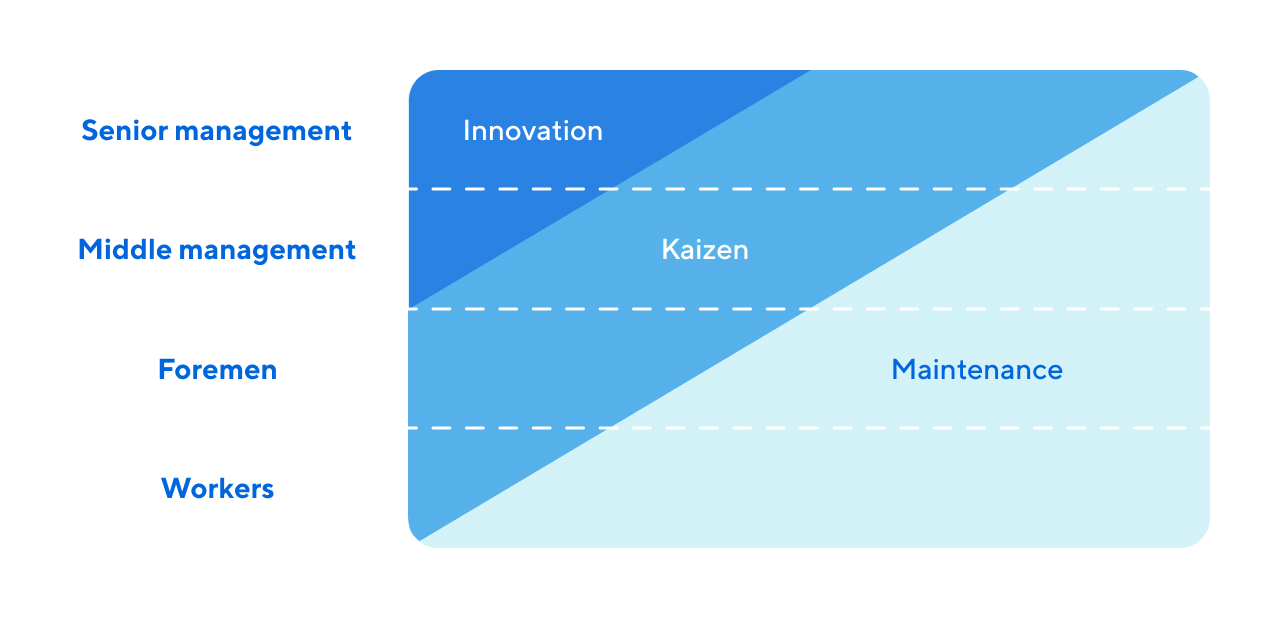
As can be seen in the diagram, top management should focus only on innovation and improvement (kaizen). Middle managers should think more about improvement. And supervisors and workers — about maintaining existing solutions (organisational, operational, process, discipline, training/development and others).
But, interestingly, almost all participants in the interaction are concerned with kaizen (improvement), just to different degrees.
Innovations are the most expensive to implement, so most changes should be made through kaizen. It is cheaper and more practical.
Process orientation
Yes, kaizen is a process-oriented methodology. The better the processes in the company, the better the quality of the final product.
But the result itself is not the most important thing. The most important thing is the process of improving it.
Planning and standardisation cycles (PDCA and SDCA)
The main cycle that drives the whole system is planning. The complete set of actions within it:
- Plan
- Do
- Check
- Act (correct)
The cycle is often referred to by the acronym PDCA.
Starting each new cycle should strive for improvement, so the process can be endless.
The SDCA cycle is used to stabilise already existing business processes:
- Standardise
- Do
- Check
- Adjust/act (Act).
SDCA is actually a maintenance cycle.
Prioritising quality
As you can see above, kaizen chooses three goals at once as its main objectives: cost, quality and delivery (logistics). But when comparing these three components, quality should be given the highest priority.
Based on facts and verified data
Any communication within the company or with external parties must be based on verified data. You can’t act on information you’re not sure of.
There are no hunches or feelings in business. Only a scientific approach matters. Every axiom or theory must be tested.
The receiving process as a consumer
Regardless of whether a business process is internal or external to the organisation, it is always considered as a real consumer of the product created in the previous step.
This means that any product created at any stage of the cycle is passed on as a real consumer. This means that the producer can vouch for the quality of the product, can provide timely feedback, accompanying documentation, etc.
Internal kaizen subsystems
This typically includes the following systems:
- Complete, total quality control. Because quality is always top priority.
- The result is always right on time. This applies to variations both up and down.
- Equipment maintenance. Tools must always be in perfect condition. Not only in terms of cleanliness and maintenance, but also when it comes to modernisation.
- The suggestion scheme is a feedback system through which rational ideas can reach senior management representatives from any lower level.
- Work in small groups. Groups can be organised according to different criteria, but the most important thing is that the purpose of their existence is aligned with the overall direction of the business and with continuous improvement.
- Policy Deployment System. In fact, it is a subsystem for controlling and setting tasks. Kaizen tasks are set according to the same criteria as in the SMART system. That is, they are as substantive as possible and have specific numerical values (as in the case of KPIs).
Will kaizen planning help our business?
This is actually a very complex issue. When implementing kaizen, it is essential that all components of the system, starting with top management, correctly understand the principles of the philosophy and are willing to follow them.
If only individual components (goals, methods, subsystems, etc.) are adopted, not only will you fail to achieve maximum efficiency, but you may even achieve the opposite effect.
The most important thing to understand is that the goal is not the end result, but the process of achieving and improving it. This can be the determining factor in implementation failure. For example, if top management decides to prioritise cost reduction or shortening the delivery cycle etc. over quality.
In any case, a lot will depend on the quality of the planning, the right setting of objectives, the control system and other factors.
To reduce the negative impact of various errors and risks, it is logical to use special automation systems. The work of managers can also be automated. For example, it can be such software solutions as BPM and CRM systems, ERP (about the difference between them), task schedulers, online calendars and not only. In our opinion, the best comprehensive tool for project management is the cloud system Projecto.